Motor drive boards are essential components in various electronic devices and systems, providing the necessary control and power to drive motors efficiently. These boards are used in a wide range of applications, from industrial machinery to consumer electronics. The production processes for motor drive boards can vary depending on the specific requirements of the application, but there are some common steps that are typically involved in the manufacturing process.
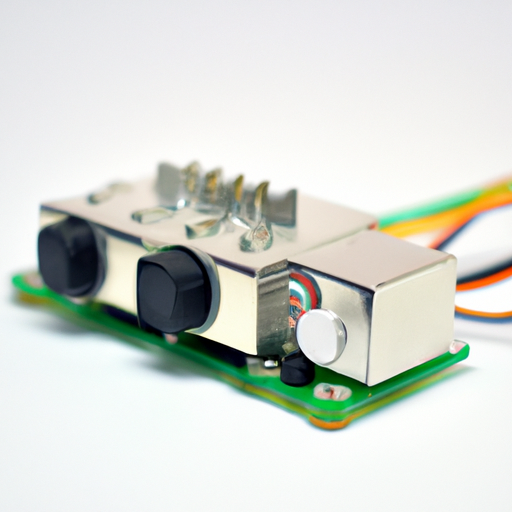
The first step in the production of a motor drive board is the design and prototyping phase. This involves creating a detailed schematic and layout of the board, taking into account the specific requirements of the motor and the control system. Once the design is finalized, a prototype board is typically produced to test the functionality and performance of the design.
2. Component selection and procurement
Once the design has been finalized and tested, the next step is to select the components that will be used in the production of the motor drive board. This includes selecting the appropriate microcontroller, power transistors, capacitors, resistors, and other components that are necessary for the operation of the board. These components are then procured from suppliers and manufacturers.
3. PCB fabrication
The next step in the production process is the fabrication of the printed circuit board (PCB) that will be used for the motor drive board. The PCB is typically fabricated using a process called etching, where a copper-clad board is coated with a layer of photoresist and then exposed to UV light through a mask that defines the traces and pads on the board. The board is then etched to remove the unwanted copper, leaving behind the traces and pads that will be used to connect the components.
4. Component placement and soldering
Once the PCB has been fabricated, the next step is to place the components on the board and solder them in place. This process is typically done using automated pick-and-place machines, which can quickly and accurately place the components on the board. The board is then passed through a reflow oven, where the solder is melted to create a strong bond between the components and the board.
5. Testing and quality control
After the components have been soldered onto the board, the motor drive board is tested to ensure that it functions correctly and meets the specifications of the design. This typically involves testing the board under various operating conditions, such as different motor speeds and loads, to ensure that it can control the motor effectively. Any defects or issues that are identified during testing are addressed and corrected before the board is approved for production.
6. Assembly and packaging
Once the motor drive board has been tested and approved, it is assembled into its final form and packaged for shipment. This typically involves mounting the board in a protective enclosure and adding any necessary connectors or cables that are required for the application. The board is then packaged in a protective box or container and shipped to the customer or end user.
Overall, the production processes for motor drive boards involve a series of steps that are designed to ensure the quality and reliability of the final product. By following these steps carefully and paying attention to detail, manufacturers can produce motor drive boards that meet the specific requirements of their customers and applications.